Adhesives provide a versatile bonding method and are used industry-wide. Whilst the bond is usually strong and durable, unfortunately bond failures can occasionally happen.
There are two main types of bond failure which commonly occur. When the adhesive separates or pulls away from one or both substrates, but does not tear, this is known as an adhesive failure. In contrast, a cohesive failure occurs when the adhesive physically separates or splits by itself.
Read on to find out our 5 top tips to avoid frustrating bond failures in future applications…
- Choose the right adhesive for your substrate
Selecting the correct adhesive is the most crucial stage to ensuring a strong, long lasting bond. Different adhesives adhere better to different substrates, therefore choosing one which is incompatible may lead to the adhesive to improperly cure. It is also important to consider the environmental and external conditions the bond will be exposed to. This includes the temperature, chemical exposure and impact or vibration.
Unsure if your chosen adhesive is correct for your application? Our Ellsworth Glue Doctor is always here to help.
- Preparation is key!
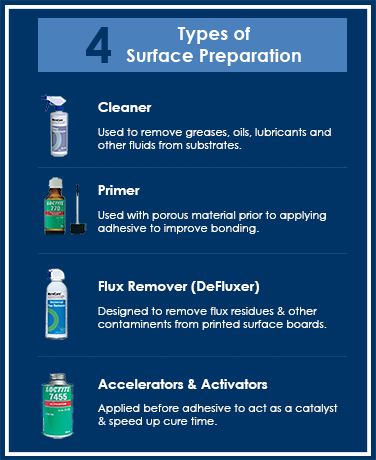
Care should be taken to ensure the substrates are ready for bonding. If a substance such as oil, grease or dirt is present it can lead to bond failure. Effective surface preparation is key to ensure optimum bonding conditions and long-term adhesion.
There are various methods and products available for surface preparation such as:
View our entire range of surface preparation products here.
- Carefully check your application requirements.
Adhesives require different actions in order for the curing process to occur. This includes factors such as cure time, cure temperature and the amount of pressure applied during the process. It is important to check each of these requirements prior to applying to the substrate and ensure you have the time and equipment required.
Furthermore, the adhesive should be applied in a consistent manner across the entire bond line to ensure an even and high strength bond. If there is too little adhesive applied, this can cause cracking or separation of the surfaces. Similarly, if too much adhesive is applied then this can take too long to set and cure causing a weak bond and an untidy finish to the substrate.
- Get Your Ratio Right!
Two component adhesives provide a strong and extremely reliable bond; however, they do often require manual mixing and preparation before they can be applied. An inaccurate mix ratio can affect the chemical properties of the adhesive and lead to a weak or failed bond. Furthermore, if the mixing process takes too long then the adhesive can become too viscous and should not be applied. Ensuring that time is taken to follow the mixing and measuring method carefully is essential with a two-component adhesive.
Unsure or struggling to maintain the exact ratio required? Our Pre-Mixed & Frozen resin service can help. Learn More.
- Don’t Stress!
Like selecting the correct adhesive for your substrate, consideration should be taken regarding the level of stress the finished bond will be faced with. Different adhesives have different levels of flexibility which can withstand stress better than others. If an adhesive cannot hold up against the joint stress, failure can occur. Adhesives such as flexible cyanoacrylates allow for a good level of movement within the joint and between substrates which can withstand this stress. Our other top picks include Robnor ResinLab PX628FF and Permabond UV670.
Additional Links:
Want to know more about surface preparation? Check out our “Guide to Surface Preparation” post for a more in-depth overview of each method.
If you have any other queries regarding bond failures or selecting the correct product for your application, please don’t hesitate to ask our Ellsworth Glue Doctor who can answer all your technical questions. Simply fill out our enquiry form.